
I'm still lost in space (pun intended) on a few things however.
Rosin soldering flux how to#
I am a welder by trade and was able to relate that to oxy-acetylene brazing with a silicon bronze rod.My welding instructor described brazing almost verbatim to that quote and that was my come to jesus moment in learning how to braze. It just won't stick." That quote was the perfect way to describe the soldering technique. "The purpose of the iron is to get the workpiece hot enough to melt the solder! Melting the solder on the iron and "dribbling" it on the work won't do at all. I've watched and read several of these how-to guides and so far, I really wish I had read this first.
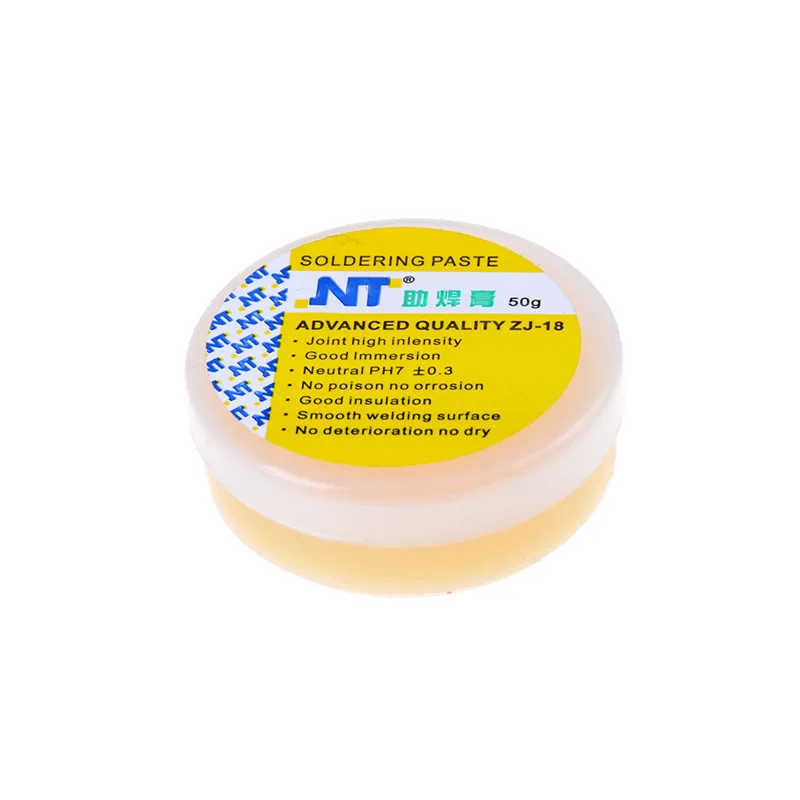
If you find any bridges, reheat and scrape off the excess solder with a small tool or the iron tip itself, or use solder wick and then resolder. It's helpful to have a diagram of what the board is supposed to look like. If your project is a PCB, inspect it carefully, using a magnifier if necessary, for solder "Bridges." These are most likely between IC pins. Solder Wick is available from the places you buy solder, and is great for soaking up excess solder if you've used too much. (You add more solder in this case for the flux.) If the solder is stuck to both the wire and pad, leave it alone and use less solder next time. Try cautiously reheating and adding a tiny bit more solder. If your PCB joint looks like a beach ball, you either didn't heat the pad and the wire, or you used too much solder. If the hole in the board isn't covered, or the joint looks dull and granular instead of smooth, reheat and add a little more solder. A good PCB joint should be shaped something like a Hershey's Kiss. How does your solder joint look? If it's smooth and shiny, and you can't see any gap between either part and the solder, it's probably good. Splice tiny wires, (for instance, adding long wires to an LED), by putting a "U" bend in each wire, then hooking them together and squeezing the connection down. Then it's easy to put a small "U" bend in the wire with your pliers and crimp that onto your terminal. If using multi-strand wire, it helps a lot to twist the end of the wire and apply a bit of solder to the wire first. Twist wires together or wrap the wire around a terminal. If soldering wires to wires, or wires to switches or other components, get a mechanically sound connection first. After only a little practice, you can solder a PCB (Printed Circuit Board) connection in 3 to 5 seconds. It takes less time to do than it does to read this. Then, apply the solder to the other side of the workpiece, not to the iron tip. Both parts must be at soldering temperature. The proper technique is to apply the soldering iron to one side of the work, making sure it's contacting both parts to be joined. The most important thing to understand about the soldering process is this: The purpose of the iron is to get the workpiece hot enough to melt the solder! Melting the solder on the iron and "dribbling" it on the work won't do at all. Preliminaries out of the way, let's start soldering. This is safer, anyway, until your skills are better. If you'll be soldering a lot of CMOS ICs (integrated circuits), they are static sensitive, and a grounded iron with a 3-prong plug will help, or just solder in IC sockets and put in the ICs when all soldering is done. You'll know when your work demands something better. The $10 one from Radio Hovel or WalMart will do just fine when you're starting out. I've been using non-temperature-controlled irons for decades, and they do just fine for all but the most demanding jobs. It does not need to be one of those fancy ones with temperature control. Your first soldering iron should be in the 25-40 Watt range. In addition, they work by putting current directly through the tip, and that current could potentially damage sensitive semiconductors.
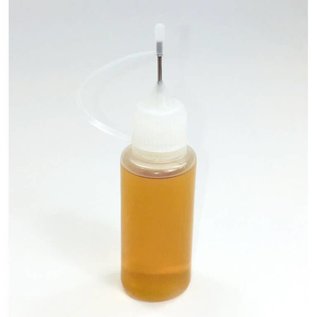
They are too imprecise and too powerful for delicate soldering. Soldering guns are designed for large, bulky projects like copper pipe or gutters. To solder electronics, you need a soldering iron, not a soldering gun.
